Safety Information
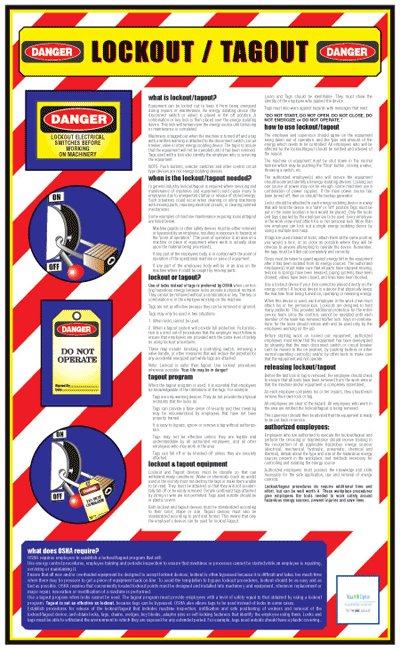
Lock Out Tag Out
Lockout-tagout (LOTO) or lock and tag is a safety procedure which is used in industry and research settings to ensure that dangerous machines are properly shut off and not started up again prior to the completion of maintenance or servicing work. It requires that hazardous power sources be "isolated and rendered inoperative" before any repair procedure is started. "Lock and tag" works in conjunction with a lock usually locking the device or the power source with the hasp, and placing it in such a position that no hazardous power sources can be turned on. The procedure requires that a tag be affixed to the locked device indicating that it should not be turned on.
Group Lock Out
When two or more subcontractors are working on different parts of a larger overall system, the locked-out device is first secured with a folding scissors clamp that has many padlock holes capable of holding it closed. Each subcontractor applies their own padlock to the clamp. The locked-out device cannot be activated until all workers have signed off on their portion of the project and removed their padlock from the clamp
In the United States a lock selected by color, shape or size (e.g. red padlock) is used to designate a standard safety device, locking and securing hazardous energy. No two keys or locks should ever be the same. A person's lock and tag must not be removed by anyone other than the individual who installed the lock and tag unless removal is accomplished under the direction of the employer. Employer procedures and training for such removal must have been developed, documented and incorporated into the employer energy control program.
Lockout-tagout in the US, has 5 required components to be fully compliant with OSHA law. The 5 components are:
1. Lockout-Tagout Procedures
2. Lockout-Tagout Training (for authorized employees and affected employees)
3. Lockout-Tagout Policy (often referred to as a program)
4. Lockout-Tagout Devices and Locks
5. Lockout-Tagout Auditing - Every 12 months, every procedure must be reviewed as well as a review of authorized employees